Billions of Scrap Tyres Roll Slowly Toward Recycling
By Sunny Lewis for Maximpact
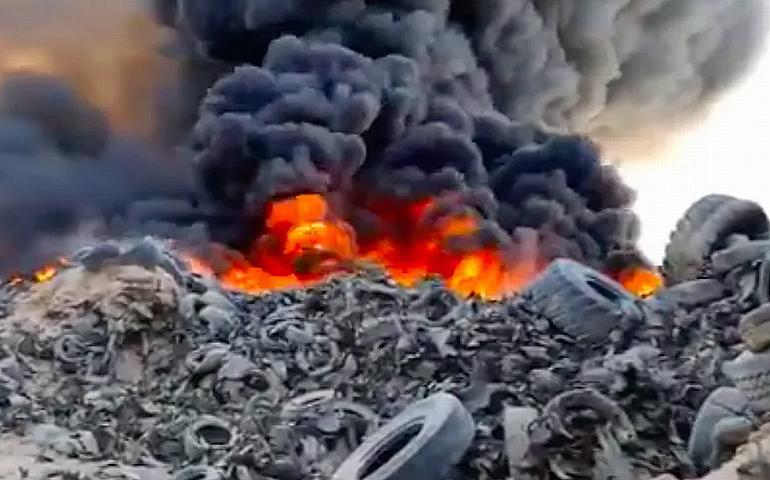
Kuwait tire fire on October 15, 2020 (Photo courtesy Interesting Engineering)
October 17, 2022 – Wherever we live on Earth, tires, or tyres, keep our world moving. Tires have a vital role to play in creating a future of mobility for everyone – a future that is environmentally friendly, efficient, safe, and accessible. Yet, tires don’t last forever, and when they reach the end of their usefulness, they become an environmental problem that takes advanced technology and much human effort to solve.
A billion end-of-life tires are generated every year and there are currently four billion such tires in landfills and stockpiles worldwide, according to a study by the Tire Industry Project for the World Business Council for Sustainable Development published in May 2021. Current estimates are even higher, reaching 1.5 billion waste tires a year according to the World Economic Forum.
The Tire Industry Project’s 11 member companies, representing more than 60 percent of the world’s tire manufacturing capacity, aims to “proactively identify and address the potential human health and environmental impacts associated with the lifecycle impacts of tires to contribute to a more sustainable future.” Current members of the Tire Industry Project are: Bridgestone, Continental, Cooper Tire, Goodyear, Hankook, Kumho Tire, Michelin, Pirelli, Sumitomo Rubber, Toyo Tires, and Yokohama Rubber.
“Recycling end-of-life tires is a major challenge for the tire industry and its customers,” French tire manufacturer Michelin says. “Around one billion tires reach the end of their useful lives each year. Recycling is part of a holistic process that includes collecting end-of-life tires, sorting them and giving them a new purpose. Around 65% of them are collected for some form of reuse, roughly 70% are recycled to recover their materials, and the remaining 30% are generally used for energy recovery.”
Last year, Michelin began construction on its first tire recycling plant in collaboration with Enviro, a Swedish company that has developed a patented technology to recover carbon black, oil, steel and gas from end-of-life tires. Based in Chile’s Antofagasta region, the $30 million plant will be able to recycle 30,000 tons of huge earthmover tires a year, or nearly 60 percent of such tires scrapped every year nationwide.
But many millions of waste tires are just dumped, and the piles of scrap tires are causing problems due to their bulk and the chemicals they can release. Tires are an unexpected source of ocean microplastics and vehicle tires, even on electric cars and trucks, produce noxious dust.
End-of-life tires pile up in landfills and are dumped illegally, contaminants leech from the dumps into local waterways, and when fires break out they emit black plumes of toxic smoke that sometimes can be seen from space.
This happens far too often, but the tire industry, government authorities, scientists and private corporations around the world are discovering and perfecting technologies to find new uses for waste tires – taking steps toward a circular economy in this industry.
World’s Biggest Tire Dump Now Being Recycled
On April 17, 2012, a fire broke out in a tire dump near Al Jahrah, Kuwait, fueled by about five million tires. The Kuwait News Agency reported that hundreds of firefighters, soldiers and employees of the Kuwait Oil Company struggled to contain the blaze.
Instruments on NASA’s Terra satellite captured an image showing the actively burning area, and thick black smoke blowing eastward from the blaze, carrying most of the smoke out to sea.
More recently, on April 29, 2021, Kuwaiti firefighters tried to control a massive fire that broke out at the world’s largest tire graveyard – containing about 50 million tires in Jahra Governorate. Seventeen years of tire dumping and three huge fires since 2012, finally prompted the authorities to shut it down completely.
“We have moved from a difficult stage that was characterised by great environmental risk,” Kuwait’s Oil Minister Mohammed al-Fares said after the tires were removed by truck to become part of a new residential area. “Today the area is clean and all tires have been removed to begin the launch of the project of Saad Al-Abdullah city.”
By September 2021 Kuwait, which wants to build 25,000 new houses on the site, finished moving all the tires to the new location at al-Salmi, near the Saudi border, where tire recycling has begun.
At a plant run by the EPSCO Global General Trading recycling company, based in Kuwait City, employees sort and shred the scrap tires, before pressing the particles into rubbery flooring tiles and other products.
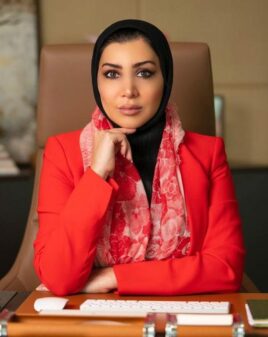
Engineer Alaa Hassan, chief executive officer of EPSCO Global General Contracting, Kuwait (Photo courtesy EPSCO) Posted for media use https://epscoglobal.com/
Engineer Alaa Hassan, head of EPSCO Global General Contracting, told reporters her firm extracts raw materials from the tires, including elements used to pave roads and sidewalks for the new city.
“The factory is helping society by cleaning up the dumped old tires and turning them into consumer products,” said Hassan. The company also exports products made of recycled tires to neighboring Gulf countries, particularly Qatar and Saudi Arabia, and to India.
“We strive to generate higher earnings while fostering a culture built on the highest ethical values, our love for Kuwait and the planet, providing alternative solution for client’s challenges while saving this planet one inch at a time,” Hassan said.
The EPSCO plant, which began operations in January 2021, can recycle up to three million tires a year through a process called pyrolysis – the heating of an organic material in the absence of oxygen. Because no oxygen is present, the material is not burned. Instead, the biomass thermally decomposes into combustible gases and bio-char.
Pyrolysis is one technology available to convert waste tires to an intermediate liquid product that can be refined to drop-in hydrocarbon biofuels, oxygenated fuel additives and petrochemical replacements – a promising approach for recycling waste tires but perpetuates the use of fossil fuels.
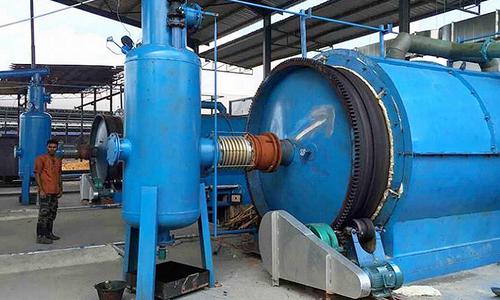
Small waste tire pyrolysis plant (Photo courtesy Tire Recycling Machines, Zhengzhou, China) https://tirerecyclingmachines.com/
According to Sheikh Abdullah Al-Sabah, director general of the Environment Public Authority, Kuwait plans to recycle all the tires and avoid the need for another landfill. “There is already a factory today that repurposes them, and we hope to find other manufacturer to contribute to help end the tires issue,” he told Agence France Presse (AFP).
Tyre Fire Pushes Europe Toward Recycling
In January 2014, some 15,000 tonnes of waste tires caught fire at a recycling plant near the city of Leeds in North Yorkshire, England in another blaze that was visible from space.
A NASA satellite caught an image of the giant fire at the Gascoigne Wood Interchange Newgen Recycling facility in Sherburn-in-Elmet, a village first settled centuries ago in Roman times.
After the disastrous fire, Newgen Recycling took tires from the Gascoigne Wood Interchange plant and turned them into rubber chippings for play areas, arenas and equestrian centers, for poultry houses and for landscaping mulch. Today, Newgen has moved to Walton-On-Thames, Surrey and recycles many different waste materials, but not tyres.
Other companies are recycling tyres. The UK Environment Agency says tens of millions of tyres are disposed of each year in the United Kingdom. They can be baled for use in construction, granulated for horse enclosures, retreaded for further use as tyres or granulated.
In the European Union, EU Directives banning landfilling of whole tyres (2003), shredded tires (2006) and vehicle end-of-life components (2008) means that Europe is at a very urgent stage to find the solution to the problem.
BlackCycle? What’s That?
Moving toward a more sustainable tyre industry, an EU-funded project has produced the world’s first sustainable carbon black (sCB) material in a circular process.
A fine carbon powder produced from the incomplete combustion of heavy petroleum products, carbon black is mainly used to reinforce tyres, making them more resistant to ultraviolet rays and prolonging their lifespan.
For the first time, in November 2021, after 18 months in existence, the consortium of the BlackCycle project, coordinated by French tyre manufacturer Michelin, welcomed 120 international industry leaders, academics, Horizon 2020 project coordinators, and politicians from 20 countries to a workshop exchange of ideas about the deployment of circular economy initiatives in Europe. They met at Michelin’s technology center at Ladoux, France.
During the workshop, the BlackCycle consortium announced the world’s first production of sustainable carbon blacks (sCB) for tire applications on a conventional carbon black furnace reactor by using oils derived from an end-of-life tire pyrolysis process. “This novel production of a sustainable material from end-of-life tyres represents a truly circular process,” BlackCycle said.
Launched in May 2020, the BlackCycle project will run until the end of August 2023 and is funded by the European Union’s Horizon 2020 research and innovation programme.
As part of the project, 13 companies from five EU countries are researching a sustainable process to recycle recovered materials from end-of-life tires back into new tire production. This includes the collection and selection of raw materials from end-of-life tires, as well as the optimization of pyrolysis, oil refining and recycling.
This year’s BlackCycle workshop will be held in Zaragoza, Spain November 22-23.
Europe is doing well at working used tyres into a circular economy, according to a 2021 report from the European Tyre & Rubber Manufacturers’ Association (ETRMA) with annual findings of a recycling-recovery rate of 93 to 95 percent in Europe, ETRMA said.
The ETRMA consolidated data from 32 nations, including the European Union, Norway, Serbia, Switzerland and Turkey, to reach that figure, it said. The remaining tyres could not be tracked down, it said.
By weight, some 1.96 million metric tons of scrap tires went to material recovery, ETRMA reported.
This included 1.47 million tons granulated to recover their rubber, steel and textiles; 326,000 tons in cement from the co-processing of tires in cement kilns; 105,000 tons in civil engineering applications; and some minor amounts for pyrolysis, steel mills, foundries and other applications.
But The European Union’s tyre recyclers are having a tough year, regardless of new technologies available to break down and repurpose end-of-life tires.
The European Tyre Recycling Association (ETRA), a pan-European body representing the independent tyre recycling sector, says Russia’s war on Ukraine has sent the cost of energy soaring, “posing serious concerns about energy availability and affordability and survival of many industries (tyre recyclers included) as well as families.”
“Tyre recyclers already are no longer able to granulate tyres owing to the price of electricity. Sports associations wonder how the infill material can migrate from the pitch to water if there is no water. Farmers say that the little water available should be used to watering crops instead of natural grass. Common people ask if this is Circular Economy,” ETRA laments on its website. “The whole issue is still unclear and contradictory.”
Swiss Technology, Another Solution
Tyre Recycling Solutions SA (TRS) was founded in Switzerland in 2013 with the aim of enabling sustainable recycling of the materials in scrap tyres. “Tyre rubber is a high-performance, engineered material that is worth a second life,” the company says on its site.
So, TRS has developed Swiss proprietary technologies to process scrap tyres into a unique specialty chemical – TyreXol™ rubber powders.
“The cornerstones of our toolbox are rubber powder functionalization technologies, powder chemical coating treatment, a unique water milling technology and intelligent compounding,” the company says.
A technology developer and integrator, TRS identifies as a creator of a circular economy – scrap tyres become rubber powders which are further transformed into new light vehicle or industrial tyres, wire and cable, seals and gaskets, footwear, or even asphalt paving.
“At the center of a transformation, we solve a hazardous waste issue, creating value for existing players of the recycling chain, providing cost-efficient new materials and unique compounding solutions,” TRS says on its website.
In many places, Chinese machinery enables waste tire recycling. In China’s Henan province, the Henan Doing Environmental Protection Technology Co., Ltd makes machinery that scrap tire recyclers depend on – waste car tire pyrolysis plants in several sizes. All the company’s products are exported to more than 90 countries in North and South America, Eastern Europe, Southeast Asia, Africa, and Oceania.
Tires Transformed Stateside
In the United States, Colorado has more scrap tires than any other state. Two massive tire monofills in Hudson and Midway – between Colorado Springs and Pueblo – account for more than 60 million tires between them. And, there are other dump sites, both legal and illegal.
Now, Roman Navarro, founder and CEO of Tires to Green Recycling in Hudson, saw an opportunity to recycle tires in Colorado after starting his career recycling electronics in Mexico.
Tires to Green Recycling has grown to 21 employees after investing “many million dollars” in its recycling facility in Hudson, 30 miles northeast of Denver, “ColoradoBiz” reported in March 2021. The facility can process 36,000 tons of tires a year, more than the market can handle. “We can do more than we can sell, and that’s a problem,” Navarro said.
California strengthened its market for recycled tire products in 2013 by mandating the use of rubber in asphalt, which typically requires 2,000 scrap tires to resurface a mile of roadway lane.
The tire shredding system for tire-derived fuel is designed to product up to 1.2-20 tons per hour. Navarro says that based on the needs of his costumers, his tire-derived fuel systems produce a 25mm to 152mm (1″-6″) rubber chip, which is used as a coal additive for industrial boilers. He says these facilities are turning to tire-derived fuel because it burns hotter and cleaner than coal and is more effective.
Tyre Recycling Down Under Yields Greener, Lighter Concrete
Engineers in Melbourne, Australia have discovered a way to replace 100 percent of the conventional aggregates in concrete, such as gravel and crushed rock, with rubber from discarded tyres that meets building codes, demonstrating a circular economic pattern.
Small amounts of rubber particles from tyres are already used to replace these concrete aggregates, but efforts to replace all of the aggregates with rubber have produced weak concretes that failed to meet the required standards – until now.
The team from the Royal Melbourne Institute of Technology (RMIT) says their new greener and lighter concrete will reduce both manufacturing and transportation costs.
Their study published in the journal “Resources, Conservation & Recycling” <DOI: 10.1016/j.resconrec.2022.106390>reveals a manufacturing process for structural lightweight concrete where the traditional coarse aggregates in the mix were completely replaced by rubber from used car tyres – disproving older theories that limited recycled rubber in concrete.
“We have demonstrated with our precise casting method that this decades-old perceived limitation on using large amounts of coarse rubber particles in concrete can now be overcome,” said lead author and PhD researcher from RMIT University’s School of Engineering, Mohammad Momeen Ul Islam.
“The technique involves using newly designed casting moulds to compress the coarse rubber aggregate in fresh concrete that enhances the building material’s performance,” he explained.
Australia does not permit the export of used tyres, making new methods for recycling and reprocessing them locally increasingly important.
Study co-author and team leader, Professor Jie Li, said this manufacturing process offers both environmental and economic benefits.
“As a major portion of typical concrete is coarse aggregate, replacing all of this with used tyre rubber can significantly reduce the consumption of natural resources and also address the major environmental challenge of what to do with used tyres,” he said. “The greener and lighter concrete could greatly reduce manufacturing and transportation costs.”
“This would benefit a range of developments,” Li said, “including low-cost housing projects in rural and remote parts of Australia and other countries around the world.”