Closing the Cycle on Single-Use Plastics
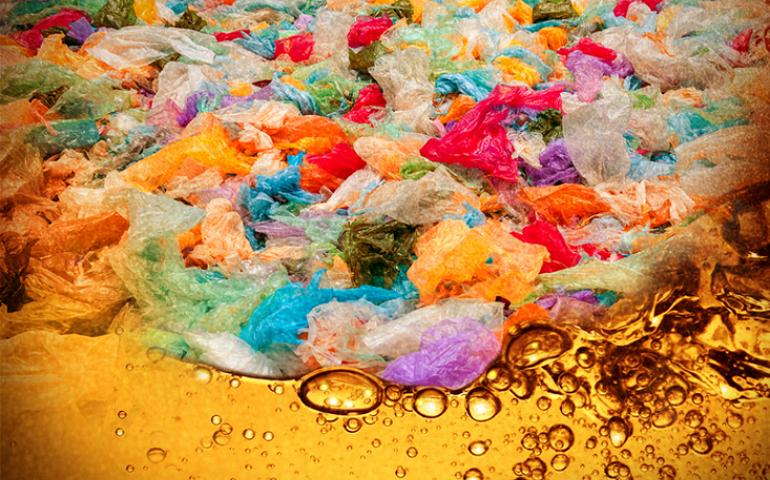
By Sunny Lewis for Maximpact
RICHLAND, Washington, February 25, 2023 (Maximpact.com Sustainability News) – Petroleum-based plastic waste is an untapped resource that can serve as the starting material for useful durable materials and for fuels. But looking at a mountain of plastic waste and seeing its value “requires an innovator’s mindset, a chemist’s ingenuity, and a realist’s understanding of the economics involved,” says an international team of scientists in describing their new research.
Typically, recycling plastics requires cracking – splitting apart the tough and stable chemical bonds that also make plastics so persistent in the environment. This cracking step requires high temperatures, making it expensive and energy intensive.
Now, an international research team, co-led by the U.S. Department of Energy’s Pacific Northwest National Laboratory (PNNL) and scientists from the Technical University of Munich, Germany, has done something new.
The team combined the cracking step with a second reaction step that immediately completes the conversion to a liquid gasoline-like fuel without unwanted byproducts, as they reported in the February 23 issue of the peer-reviewed journal “Science.” <10.1126/science.ade7485>
“Left alone, plastics don’t really break down; they just break up,” quips editorial staff writer Courtney Lindwall, explaining the problem on the nonprofit Natural Resources Defense Council website. “Over time, sun and heat slowly turn plastics into smaller and smaller pieces until they eventually become what are known as microplastics.”
“These microscopic plastic fragments, no more than 5 millimeters long, are hard to detect – and are just about everywhere … microbeads used in facial scrubs or the microfibers in polyester clothing. They end up in the water, eaten by wildlife, and inside our bodies,” writes Lindwall. “They’ve even made their way up to the secluded Pyrenees mountain range and down to the bottom of the Mariana Trench.”
At the same time, there are potentially useful raw materials bound up in the 400 million tonnes of plastic waste humans produce every year – plastic grocery bags, food packaging, bottles, wrappers, straws, cups, cutlery. But it has been much cheaper to keep making more of these single-use plastics and throwing them away than to recover, recycle or upcycle them.
“Cracking just to break the bonds results in them forming another one in an uncontrolled way, and that’s a problem in other approaches,” said Oliver Gutierrez, a study author and chemist at PNNL.
“The secret formula here is that when you break a bond in our system, you immediately make another one in a targeted way that gives you the end product you want. That is also the secret that enables this conversion at low temperature,” Gutierrez said.

Johannes Lercher, a senior author of the study, director of PNNL’s Institute for Integrated Catalysis, also serves as professor of chemistry at the Technical University of Munich. “This study points to a practical new solution to close the carbon cycle for waste plastic that is closer to implementation than many others being proposed,” Lercher said.
“To solve the problem of persistent waste plastic, we need to reach a critical point where it makes more sense to collect it and return it to use than to treat it as disposable,” he said. “We’ve shown here that we can make that conversion quickly, at mild conditions, which provides one of the incentives to move forward to that tipping point.”
In their study, the researchers do note limitations on the types of plastics their method can handle.
The process works for low-density polyethylene products (LDPE, plastic resin code #4), such as plastic films and squeezable bottles, and polypropylene products (PP, plastic resin code #5) such as food containers used for yogurt, sour cream and margarine, that are not typically collected in curb-side recycling programs in the United States.
High-density polyethylene (HPDE, plastic resin code #2) would require a pretreatment to allow the catalyst access to the bonds it needs to break. HDPE plastic is the stiff material used to make milk jugs, detergent and oil bottles, toys, and some plastic bags.
Now You See It, Now You Don’t
Today scientists around the world are applying their expertise to efficiently breaking the chemical bonds that give plastics characteristics such as durability, pliability, and water resistence.
For instance, a Hong Kong start-up company, has launched an eco-friendly plastic bag dubbed “Invisible Bag” that dissolves in hot, but not boiling, water – above 80 degrees Celsius (176°Fahrenheit). The boiling point of water is 100 degrees Celsius or 212 degrees Fahrenheit at sea level.
Invisible Bag <https://www.invisible-company.com/> ingredients are non-toxic and will not cause harm to the environment, the company asserts.
Distinctive Action, the company that makes the Invisible Bag, was started by Devana Ng and her husband Flavien Chaussegros, who are passionate about trail running. In 2019, they encountered mountains of plastic waste and decided to do something to change the situation, so they founded the company to promote sustainable and environmentally friendly products.
The Invisible Bag might look like plastic, and function like plastic, but it’s not plastic. This dissolving bag is made of polyvinyl alcohol (PVA) with plant-based starch, glycerin and water. To watch a 10 second video that shows it dissolving in hot water, click here. <https://en.pinkoi.com/product/gCvEZrM4>
PVA is used in water-soluble films that wrap many products used in kitchens, laundry rooms, bathrooms, and medical offices. PVA might look like plastic, but it’s not. It’s a food-grade material that is colorless, water-soluble and designed to biodegrade after use, unlike plastic.
After soaking in hot water for a few minutes, the Invisible Bag will dissolve, without forming micro-plastics, because it isn’t plastic.
As a synthetic polymer manufactured from acetic acid and ethylene, PVA is usually derived from fossil fuels, though it is possible to source ethylene made from renewable, bio-based sources.
Because of PVA’s biodegradability, the U.S. Environmental Protection Agency’s Safer Choice program recommends it as product that’s safe for people and for the environment. The Safer Choice label means that a product meets strict criteria around human safety and environmental impact.
The U.S. Food and Drug Administration has also approved it as a safe ingredient for healthcare products like eye drops, over-the-counter pharmaceutical capsules, vitamins, food, household items, and beauty products.
Solubag’s Bio-based Non-Plastic
Originally formed in Chile in 2014, Solubag® is a group of companies at a global level made up of Chilean researchers, and managing partners, who have the support of international investors, in their quest for non-toxic bio-based PVA.
Now also in the United States as Solubag USA, this tech development company has created a biodegradable, dissolvable plastic alternative made of PVA that is eco-friendly because it is not made from fossil fuels.
Founders Roberto Astete and Cristian Olivares, researchers from Chile, discovered the formula while experimenting with biodegradable detergent.
Solubag contains polyvinyl alcohol, which is usually made from crude oil, however, Astete and Olivares found another way, using natural substances. This results in an environmentally friendly, water-soluble substance.
Solubag’s products range from thick to thin and from cold-water soluble to hot-water soluble. The nontoxic Solubag is edible and dissolves within minutes when stirred into water. After only three minutes of being submerged, the bag is gone.
“Our product comes from a limestone that does not hurt the environment,” explains Astete. “What remains in the water is carbon that has no effect on the human body.”
Today, Solubag offers all kinds of bio-based PVA bags and has made PVA face masks for personal care, as well as for the care of loved ones, the only masks that provide protection to the users and protect the environment when they are discarded.
Astete and Olivares said, “The main difference between traditional plastic and ours is that traditional plastic remains between 150 and 500 years in the environment and ours only lasts minutes. You can decide when to destroy it.”