Electric Aviation Speeds Toward Takeoff
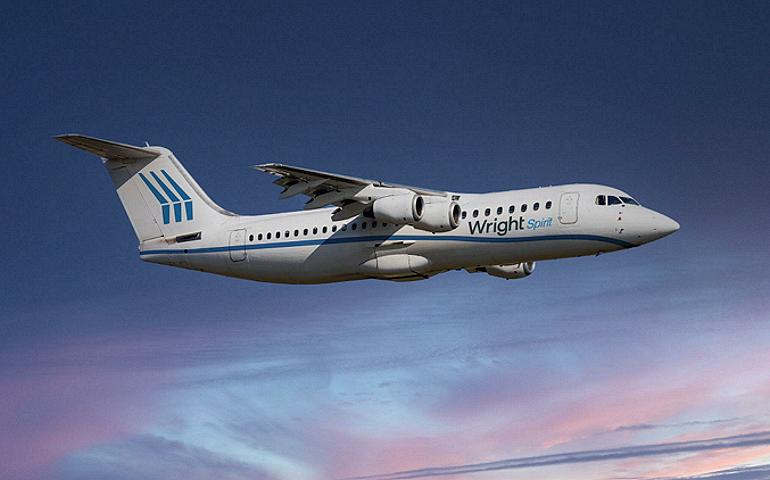
By Sunny Lewis for Maximpact
MONTEREY, California, September 30, 2023 (Maximpact.com Sustainability News) – The aviation industry is moving briskly toward market takeoff for electric commercial aircraft, and many companies on the front lines of these new technologies are developing them cooperatively. From a battery-powered 186-seat commercial passenger jet to smaller hydrogen fuel cell regional planes, electric aircraft are arriving shortly. Have your boarding passes ready!
Most aircraft engines today run on fossil fuels like Jet A, Jet A1, Avgas, or diesel <https://www.amspecgroup.com/news/types-of-jet-fuel/>, but new electric flight technologies are about to change the way we view aircraft propulsion, if they haven’t already.
In fact, under climate-change pressure to decarbonize aviation, creativity is flourishing. “Around the globe, around 215 electrically-propelled aircraft are currently in development. We are now witnessing an age of innovation in aerospace and aviation of a type not seen for decades,” writes Robert Thomson, a partner in the Munich=based international management consultancy Roland Berger.
Industry experts say electric airplanes will be in ordinary use before the end of the next decade.
Right now, the Wright 1, an all-electric, 186-seat commercial passenger jet with an 800-mile range, is being developed by UK budget carrier easyJet in partnership with U.S. startup Wright Electric <https://www.weflywright.com/aircraft> of Monterey, California. Plans call for the electric jet to enter service around 2030.
For wheels up even sooner, Wright Electric announced in November 2022 its plans for an electric 100-seater, the Wright Spirit, due out in 2026. The first commercial flights by a major airline in this plane, planned by United Airlines, are set for 2026.
The Wright Spirit builds on a four-engine, 100 passenger platform – the British Aerospace 146 (BAe 146). The short-haul, regional airliner was manufactured in the United Kingdom by British Aerospace, later part of BAE Systems, from its first flight in 1981. Evolving through many variants and phaseouts, by July 2020, just 54 BAe 146s and their cousins, Avro RJ aircraft, were in airline service, with another 70 of the planes in storage.
Electric airplanes use battery power to drive electric motors that propel the aircraft. Powered by rechargeable batteries, charged before each flight, the Wright aircraft will be able to handle flights of under 300 miles. It will feature high aspect-ratio wings for energy efficient flight, distributed electric propulsion and swappable battery packs with advanced cell chemistry.
Wright says the propulsion system can be used as a motor or as a generator, so it can be configured as a turbogenerator or an auxiliary power unit for high altitude power in commercial or defense applications.
In June 2023, Wright Electric announced at the Paris Air Show that the company has achieved 1 Megawatt (1,300 horsepower) with its revolutionary aerospace electric motor-generator.
That means that by 2040, Wright says it will eliminate carbon emissions from all flights under 800 miles.
Jeff Engler, founder and CEO of Wright Electric, explained, “Achieving 1 Megawatt, specifically 1 Megawatt of shaft power, is an important step in reaching Wright’s goal of making all single-aisle flights under 800 miles zero emissions. Commercial class airplanes need megawatt-sized propulsion systems for a full passenger load take off.”
Wright has worked on development programs with NASA, the U.S. Department of Energy, the U.S. Army, and the U.S. Air Force in its motor and generator development efforts. Engler announced that the company has signed a Space Act Agreement with NASA to conduct altitude testing at its NASA Electric Aircraft Testbed in Sandusky, Ohio. ” We are excited to bring our motor to the NEAT facility at NASA, where it will be tested at up to 40,000 feet, and we are confident our motor is more than ready for that challenge,” he said.
By leveraging Wright’s megawatt-class propulsion system, the company has transformed the BAe 146 into an all-electric, zero-emissions aircraft specialized for one-hour flights on some of the world’s busiest passenger routes.
In Europe, Wright says that the first routes for the Wright Spirit will be:
Frankfurt-Paris
Paris-London
Stockholm-Copenhagen
Lisbon-Madrid
In the Americas:
Brazil: Sao Paulo-Rio de Janeiro
United States:
New York-Boston
New York-Washington
San Francisco-Los Angeles
Atlanta-Orlando
In the Middle East:
Doha-Dubai
Istanbal-Izmir
Riyadh-Medina
In Asia:
Sydney-Melbourne
Hong Kong-Taipei
Kuala Lumpur-Singapore
Tokyo-Osaka
Seoul-Jeju
United Airlines announced in July that the company is purchasing 100 zero-emission, 19-seater, electric planes from Swedish startup Heart Aerospace for short flights in the United States in 2026.
Heart Aerospace and American aerospace technology giant Honeywell, have announced a collaboration to integrate Honeywell’s next-generation flight control system into the new ES-30 regional electric airplane.
Swedish investment and aircraft leasing company Rockton will acquire up to 40 of Heart Aerospace’s 30-passenger ES-30s. They will have a fully electric zero emissions range of 200 kilometers (124 miles), an extended hybrid range of 400 kilometers (248 miles) with 30 passengers, and flexibility to fly up to 800 kilometers (500 miles)with 25 passengers.
Denmark and Sweden have announced plans to make all domestic flights fossil fuel-free by 2030. “The Nordic region will be a leader in the adoption of electric aviation with several concrete infrastructure projects already underway. As a Swedish leasing company, Rockton is clearly a part of this pioneering spirit and we’re happy to have them as a partner,” said Simon Newitt, chief commercial officer, Heart Aerospace.
BAE Systems and Heart Aerospace are collaborating to define the battery system for Heart’s ES-30 electric airplane.
The battery will be the first of its kind to be integrated into an electric conventional takeoff and landing regional aircraft, allowing it to efficiently operate with zero emissions and low noise.
“Our industry-leading solution builds on decades of expertise delivering technologies and systems needed to progress sustainable transportation,” said Ehtisham Siddiqui, vice president and general manager of controls and avionics solutions at BAE Systems. “We are delighted to collaborate with Heart Aerospace on the innovative battery system for its electric airplane.”
The program will leverage more than 25 years of BAE Systems’ expertise in electrifying large, heavy-duty industrial vehicles. Today, the company has over 15,000 power and propulsion systems operating in service across the globe. Work on the program will be conducted at the BAE Systems state-of-the-art facility in Endicott, New York.
“BAE Systems’ extensive experience in developing batteries for heavy-duty ground applications, and their experience in developing safety critical control systems for aerospace, make them an ideal partner in this important next step for the ES-30 and for the aviation industry,” said Sofia Graflund, chief operating officer at Heart Aerospace. “We look forward to decarbonizing air travel together.”
U.S. Military Keen on Electricity-Powered Flight
In the United States, accelerated innovation for technologies such as electric aircraft propulsion is being facilitated through the U.S. Secretary of the Navy’s “Climate Action 2030” policy, which prioritizes the development of systems not dependent on fossil fuels, expanding the use of renewable energy and electric propulsion.
In addition to supporting Climate Action 2030 and similar policy goals, electric aircraft propulsion can enable new design freedoms and functions, leading to lower energy consumption and higher propulsion efficiency.
The signature noise of petrol-powered airplane engines could be all but eliminated with electric aircraft propulsion, enhancing the military stealth capabilities of future systems.
In 2020, the U.S. National Aeronautics and Space Administration (NASA) asked the Naval Postgraduate School to solve a critical barrier to the development of electric aircraft propulsion – the creation of a circuit breaker that could support large electric platforms running on direct current (DC) electricity.
In March, a successful test of the Navy High Speed Solid-State Fault Management System for electric aircraft propulsion confirmed their breakthrough results.
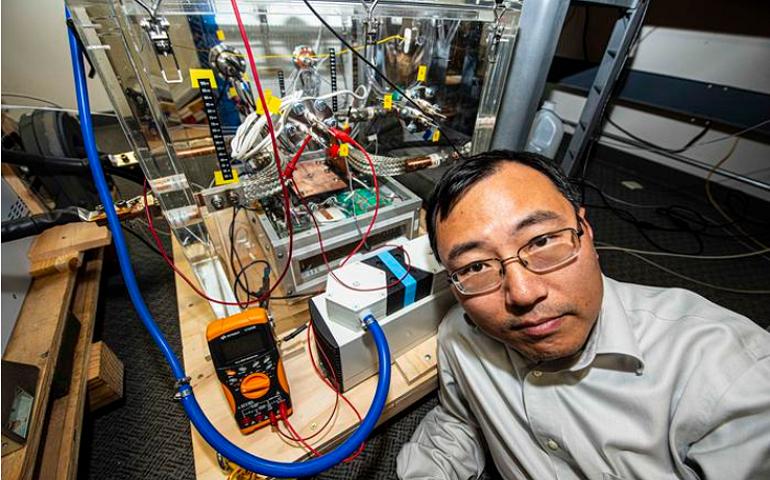
The research and design of the DC circuit breaker for electric aircraft propulsion was led by Dr. Di Zhang, associate professor of electrical and computer engineering at the Naval Postgraduate School, along with a team of NPS students.
Dr. Zhang, who has designed electric power converters with General Electric’s Global Research Center, is widely considered an expert on large electric vehicles. NASA awarded him a US$750,000 research grant to continue his research to refine the weight and performance of the team’s initial circuit breaker design.
Electric aircraft propulsion is one of many emerging technologies receiving increased attention from the Secretary of the Navy Carlos Del Toro, who is accelerating innovation throughout the the U.S. Navy.
“We are indeed in an innovation race – and it is one we must win,” said Del Toro during remarks at the Naval Research Laboratory in Washington, DC, on September 28. “Innovation must permeate every aspect of our department’s approach to the delivery of the technologies and capabilities at a speed and scale necessary for our Navy and Marine Corps to confront the challenges of today and the future.”
Accelerated innovation for technologies such as electric aircraft propulsion is facilitated through the Secretary of the Navy’s “Climate Action 2030” policy, which prioritizes the development of systems that are not dependent on fossil fuels.
“Electric propulsion technology is crucial for future Navy capabilities, offering enhanced design flexibility, supporting power-intensive advanced systems, and ensuring stealth, efficiency, and adaptability in evolving naval environments,” said Dr. Zhang. “The technology’s integration also paves the way for the adoption of emerging energy sources, solidifying the Navy’s technological edge.”
Zhang says a fundamental question when looking at using electric power for flight is the distinction between products that run on direct current (DC) and those that run on alternating current (AC).
“A hundred years ago, Nikola Tesla and Thomas Edison had a battle over the advantages of AC versus DC electric power. Tesla won, and now much of what we use and see is running on AC power,” said Zhang.
There are advantages to using AC electricity, he says. AC generators are the primary source of electric power, driven by steam, nuclear, or other power sources. AC can be transmitted across great distances and easily changed to different voltage levels through the use of transformers. AC has an alternating current that runs in a sine curve pattern; this makes AC electricity relatively safe and easy to interrupt with a circuit breaker as the waveform naturally crosses zero.
Direct current has its own advantages that are rising in importance for future technologies. DC systems require less cabling and can be smaller and lighter than AC systems, as well as more power efficient. Clean sources of energy, like wind and solar, store power in photovoltaic grids and batteries which are inherently DC compatible.
One thing that does not get smaller and lighter with DC systems is the circuit breaker. The challenge that NASA posed to Dr. Zhang’s team was to create a circuit breaker that could shut down an electric aircraft running at maximum power in a safe, simple, and size-efficient way.
“The trend we’re seeing in energy industries and in electric vehicles is this switch to DC, and that’s why it is so important to look towards this electric aircraft design,” explained Dr. Zhang.
“With DC, we can make a design lighter and smaller with the same power which is critical for aviation and Navy applications. The target for this DC breaker design is to get the same amount of power while cutting the weight to one tenth of what’s been developed,” he said.
“Think of electricity flowing like water through a pipe. A circuit breaker is the tool you need to shut that water off. With DC, high amounts of current and voltage equate to a huge flow of water that is hard to shut down quickly,” explained U.S. Marine Corps Capt. Michael Smith, an Naval Postgraduate School electrical engineering graduate who worked on the project with Zhang.
“That quick change from a high to low voltage, or high to low current, creates an electromagnetic field that can interfere with other electric systems,” he said.
The U.S. Air Force and the U.S. Army, too, are keeping their eyes on the electric aircraft technology.
Since its start in 2020, the Air Force’s Agility Prime program has awarded more than US$100 million in contracts for electric aircraft technology, with four company recipients achieving military airworthiness, according to Avionics International. <https://interactive.aviationtoday.com/avionicsmagazine/january-february-2022/the-u-s-air-force-agility-prime-program-progress-in-2021-and-goals-for-2022/>
The Army has had “pockets of activity in this technology area for quite some time,” David Friedmann, an aerospace engineer with the Army Combat Capabilities Development Command Aviation and Missile Center’s Technology Development Directorate, said in an interview.
Here Comes Hydrogen
More attention should be given to hydrogen as a way of decarbonising air travel, urges a group of UK aviation and renewable energy companies.
On September 5, companies in the UK aviation and renewable energy sectors, including easyJet, Rolls-Royce, Airbus, Ørsted, GKN Aerospace and Bristol Airport, established the Hydrogen in Aviation (HIA) Alliance to accelerate the delivery of zero carbon aviation. HIA will work to ensure the UK capitalises on the “huge opportunity hydrogen presents to both the aviation industry and country as a whole.”
Hydrogen can either be burned in a jet engine or it can be used to power a fuel cell to generate electricity to power an electric propulsor. Hydrogen tanks have to be housed in the fuselage of aircraft or be supported by the wing structure.
Hydrogen can be produced with low-carbon power and when burned produces zero emissions, reducing the environmental impact of aviation. Aircraft maker Boeing recognizes the technology’s potential and Airbus plans to launch a first commercial hydrogen-powered aircraft by 2035. Global management consulting firm McKinsey & Company predicts that hydrogen aircraft would enter the market in the late 2030s, accounting for a third of aviation’s energy demand by 2050.
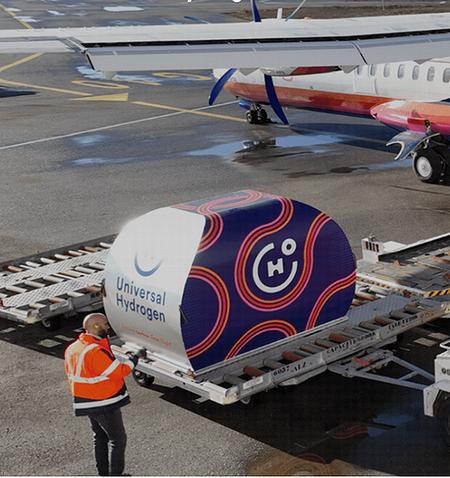
Hydrogen aviation took its first flights this year. Startups ZeroAvia and Universal Hydrogen, both headquartered in California, spent the first half of the year demonstrating and testing some of the world’s first hydrogen fuel-cell aircraft.
“With up to 60 times greater specific energy and lower cycling costs than lithium-ion batteries and numerous advantages over all other decarbonisation solutions, hydrogen-electric powertrains are the only viable, scalable solution for zero-emission aviation,” says ZeroAvia, which has operations in the states of California and Washington and in England at Cotswold Airport and in London.
The company is initially targeting a 300-mile (482km) range in 9–19 seat aircraft by the end of 2025, and up to 700-mile (1,126 km) range in 40–80 seat aircraft by 2027. Looking ahead to 2040, ZeroAvia envisions 200+ seats in a hydrogen-powered aircraft with a 5,000 mile (8,046km) range.
Universal Hydrogen this year conducted test flights that took a hydrogen-powered plane to 10,000 feet with one of the plane’s two engines powered by hydrogen fuel cells and the other by conventional fuel due to testing safety protocols. This was the highest altitude yet reached by a commercial-scale aircraft using hydrogen propulsion.
Universal Hydrogen’s first product is a conversion kit for existing regional aircraft, starting with the ATR72 and the De Havilland Canada Dash-8, to fly on hydrogen. This consists of a fuel cell electric powertrain that replaces the existing turboprop engines.
The kit is built ot accommodate, in the rear of the fuselage, the company’s proprietary, lightweight, modular hydrogen capsules. They are transported from green hydrogen production sites to the airport and loaded directly into the aircraft using the existing intermodal freight network and cargo handling equipment.
Flying on Liquid Hydrogen
And now for something entirely new. On September 7, H2FLY, the Stuttgart, Germany-based developer of hydrogen-electric powertrain systems for aircraft, announced successful completion of the world’s first piloted flight of an electric aircraft powered by liquid hydrogen.
Four flights were completed with H2FLY’s piloted HY4 demonstrator aircraft, fitted with a hydrogen-electric fuel cell propulsion system and cryogenically stored liquid hydrogen that powered the aircraft. Their longest test flight lasted for over three hours.
Results of the test flights indicate that using liquid hydrogen in place of gaseous hydrogen will double the maximum range of the HY4 aircraft from 750 km to 1,500 km, marking a critical step towards the delivery of emissions-free, medium- and long-haul commercial flights.
“This achievement marks a watershed moment in the use of hydrogen to power aircraft. Together with our partners, we have demonstrated the viability of liquid hydrogen to support medium and long-range emissions-free flight,” said Professor Josef Kallo, co-founder of H2FLY.
“We are now looking ahead to scaling up our technology for regional aircraft and other applications,” he said, “beginning the critical mission of decarbonizing commercial aviation.”
Overall, “The trick to reaching industry standards is in the balance,” says Dr. Zhang of the U.S. Naval Postgraduate School. “You need to design something new, but not too new or it is unproven and risky. You cannot only be innovative; you must also be practical.”